
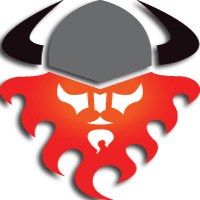
Many SOLIDWORKS customers are already enjoying the benefits of surfacing with the Sub-D modeling approach of 3D Sculptor on the 3DEXPERIENCE platform®. The curves that drive NURBS surfaces can be any degree: 1st (planar surfaces), 2nd (cylinder or conical), and 3rd (B-rep). Due to this method of generating geometry, surfaces can be precise as there is actual math driving the shape of the splines this is why you can dimension it and constraint it. Surface geometry is solved literally with a network of splines driving the shape of the surface. Parametric modeling is based on NURBS (Non-Uniform Rational B-splines). Plus, the constraints used in parametric modeling ensure that any modifications made to the design are done so with design intent in mind. You can embed intelligence in a design these “smart” solids make it easy to share with other engineers who can quickly ascertain design intent. SOLIDWORKS® customers know all about the power of parametric modeling where you can drive geometry parametrically with dimensions-change one thing and the entire model updates automatically, no need to redraw models. Taking a closer look at each technology will help to reveal what approach might be best for your projects.

Both technologies-subdivision and parametric modeling-have pros and cons. The resulting model consists of geometry created using both parametric and subdivision technologies. However, most often, models created with subdivision surfacing techniques are augmented with parametric features such as holes, chamfers, ribs, shell features, and more. Models created using subdivision modeling techniques often go directly to production without re-creating the model using parametric surfacing techniques. Often people assume that Sub-D modeling is only for the concept phase of the design, but this is not true. By leveraging subdivision (Sub-D) modeling, you can streamline the idea or conceptual stage of design because you don’t have to set up all the sub-structure (curves, surfaces, etc.) necessary in parametric modeling.īoth parametric modeling and subdivision modeling techniques are used to create the final models that will go into production. If it takes you all day to create one concept and another day to modify it, you are two days in and still on that first concept. Organic shapes are challenging to build with parametric modelers. Because of this, especially during the concept phase of design, you typically want to make several models quickly to get a clearer idea of what your customer wants. The visual appeal of a product often plays a huge role in its popularity. As we increase or decrease this iterations field, we increase or decrease the level of detail.More and more engineers and designers are being called on to develop the look and feel of new products.
BLACKSMITH3D SUBDIVISION SURFACES 2017 ISO
Let's go into the open subdiv modifier here that's actually doing the smoothing effect and disable iso line display and now we can see the actual polygons of the subdivided surface. And what we're seeing here are the so-called iso lines or the most important lines on the model. I can disable that and let's enable edge faces in the view here with F4. I'll select the chair seat, go to the modify panel, and I've got a shell modifier in there to give it some thickness. This is a polygon- based method for creating smooth, flowing surfaces such as this chair or any character or creature that has an organic, flowing shape. In the following chapter, we'll look at a modeling technique known as subdivision surfaces.
